Nanotechnology: Containment Strategies and Engineering Controls
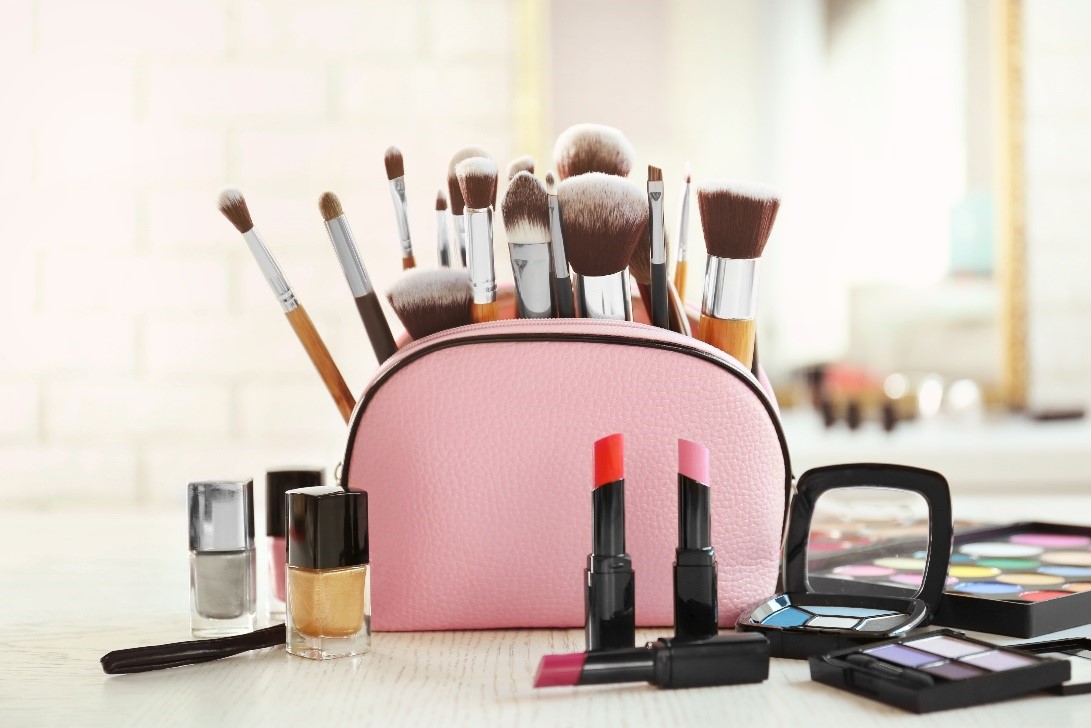
Control measures for nanoparticles, dusts, and other hazards should be implemented within the context of a comprehensive occupational safety and health management system [ANSI/AIHA 2012]. The critical elements of an effective occupational safety and health management system include management commitment and employee involvement, worksite analysis, hazard prevention and control, and sufficient training for employees, supervisors, and managers.
In developing measures to control occupational exposure to nanomaterials, it is important to remember that processing and manufacturing involve a wide range of hazards. Conducting a preliminary hazard assessment (PHA) encompasses a qualitative life cycle analysis of an entire operation, appropriate to the stage of development:
- Chemicals/materials being used in the process
- Production methods used during each stage of production
- Process equipment and engineering controls employed
- Worker’s approach to performing job duties
- Exposure potential to the nanomaterials from the task/operations
- The facility that houses the operation
PHAs are frequently conducted as initial risk assessments to determine whether more sophisticated analytical methods are needed and to prepare an inventory of hazards and control measures needed for these hazards. As part of the assessment, the health and safety professional should evaluate the magnitude of the emissions (or potential emissions) and the effects of exposure to these emissions. PHAs are an important first step toward developing control measures that can be considered during the planning stage. Essentially, hazard control should be an integral component of facility, process, and equipment design and construction. This includes design for inherent process safety. The use of engineering controls should be considered as part of a comprehensive control strategy for hazards associated with processes/ tasks that cannot be effectively eliminated, substituted for, or contained through process equipment modifications.
- Prevention through Design (PtD)
The concept of Prevention through Design (PtD) is to design out or minimize hazards, preferably, early in the design process. PtD is also called inherent or intrinsic safety, safety by design, design for safety, and safe design. When PtD is implemented, the control hierarchy is applied by designers (e.g., engineers, architects, industrial designers) and business leaders (e.g., owners, purchasers, managers) who consider the benefits of designing safety into things external to the worker to prevent work-related injuries and illnesses.
Other PtD strategies can be considered:
- Limiting process inventories by producing the nanomaterials as they are consumed in the process.
- Operating a process at a lower energy state (e.g., lower temperature or pressure), which typically results in lower fugitive emissions and therefore safer operation.
- Using fail-safe devices where possible. Fail-safe devices are designed so that if they fail, the system reverts to a safer condition. An example of a fail-safe device is a valve controlling a reagent for a reaction. If the safe condition for the system is for this valve to be closed, the fail-safe valve would automatically close in the event of a failure.
- Installing a closed transport system to eliminate worker exposures during transport activities.
PtD strategies typically do not include administrative controls and personal protective equipment (PPE) as the primary controls. These measures require worker interaction with the process or active steps to limit the extent of the hazard. Most effective PtD approaches reduce or eliminate hazardous conditions without relying on input from workers. Humans are generally recognized as being much less reliable than most machines, particularly in emergencies [Kletz 2001]. The use of administrative controls and PPE in PtD strategies is generally for redundancy—further safeguards should the primary control fail.
- OELs as Applied to Nanotechnology
Occupational exposure limits (OELs) are useful in reducing work-related health risks by providing a quantitative guideline and basis to assess the worker exposure potential and the performance of engineering controls and other risk management approaches. Currently, no regulatory standards for nanomaterials have been established in the United States. However, NIOSH has recently published two current intelligence bulletins (CIBs) regarding occupational exposures to nanomaterials. In a CIB on titanium dioxide (TiO2 ), NIOSH recommends exposure limits of 2.4 mg/m3 for fine TiO2 and 0.3 mg/m3 for ultrafine (including engineered nanoscale) TiO2 , as time-weighted average (TWA) concentrations for up to 10 hours per day during a 40-hour work week [NIOSH 2011]. In a CIB on carbon nanotubes and nanofibers, NIOSH recommends that worker exposure be limited to no more than 1 µg/m3 [NIOSH 2013].
1.3.3 Control Banding
Control banding is a qualitative risk characterization and management strategy, intended to protect the safety and health of workers in the absence of chemical and workplace standards. Control banding groups workplace risks into hazard bands based on evaluations of hazard and exposure information [NIOSH 2009b]. Note that control banding is not intended to be a substitute for OELs and does not alleviate the need for environmental monitoring or industrial hygiene expertise.
To determine the appropriate control scheme, one should consider the characteristics of the substance, the potential for exposure, and the hazard associated with the substance. Four main control bands, based on an overall risk level, have been developed:
- Good industrial hygiene (IH) practice, general ventilation, and good work practices
- Engineering controls including fume hoods or local exhaust ventilation
- Containment or process enclosure allowing for limited breaks in containment
- Special circumstances requiring expert advice
Engineering Controls
- Work with nanomaterials in ventilated enclosures (e.g., glove box, laboratory hood, process chamber) equipped with high-efficiency particulate air (HEPA ) filters.
- Where operations cannot be enclosed, provide local exhaust ventilation (e.g., capture hood, enclosing hood) equipped with HEPA filters and designed to capture the contaminant at the point of generation or release.
Reference:
Current Strategies for Engineering Controls in Nanomaterial Production and Downstream Handling Processes, Department of Health and Human Services, Centers for Disease Control and Prevention, National Institute for Occupational Safety and Health