Esco provides a one-stop solution for your equipment: from installation to upkeep!
Technologies are subject to wear and tear, so it is essential that industries will have easy access to preventive maintenance services as well as their replacement parts. We offer service contracts to ensure that any failed or deteriorated parts are replaced with identical components to retain functionality.
Esco’s 40 local offices in over 25 countries ensure real-time provision of aftermarket support for all clients. Esco has highly-trained service engineers deployed worldwide for the comfort and security of the clients.
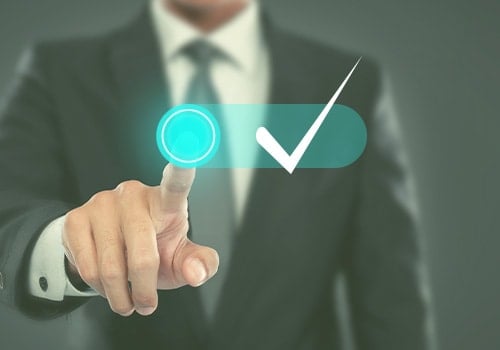
A certified process ensures that internationally compliant equipment is used pursuant to validated Standard Operating Procedures (SOPs). Those SOPs that are applicable to equipment and instruments are classified as follows:
-
Installation Qualification (IQ) documents specify the receipt and proper installation of an equipment in a suitable environment.
-
IQ is required for equipment installation, relocation, reconnection to modified sytems, and when established SOPs are changed.
IQ can be performed by the customer or Esco.
-
Operational Qualification (OQ) document proves that the equipment meets the correct specifications after installation.
-
OQ can be performed by either Esco itself or the client, and it must be done annually.
Esco provides instructions for each product’s IQ and OQ procedures. Our team of specialized engineers can perform these services directly on behalf of the customers, or arrange them with independent approved local certifiers. The availability may vary from country to country and region to region. Also, Esco can train customer employees to perform IQ/OQ.
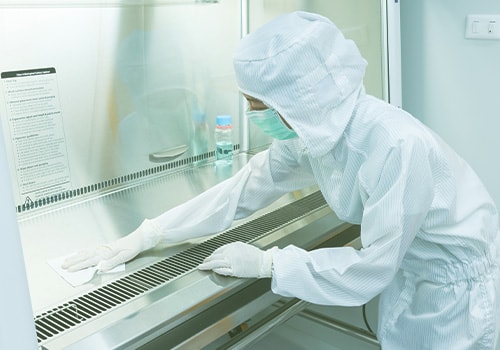
Proper operation of Esco products usually require periodic maintenance and/or decontamination in accordance with common Standard Operating Procedures and recognized laboratory safety protocols.
Decontamination is a process that reduces contaminants to acceptable levels in biological safety cabinets (BSCs) or isolation technologies, to eliminate their disease causing capabilities. Cycle development of decontamination/fumigation using formaldehyde, hydrogen peroxide or other agents, should only be carried out by trained personnel with proper equipment knowledge.
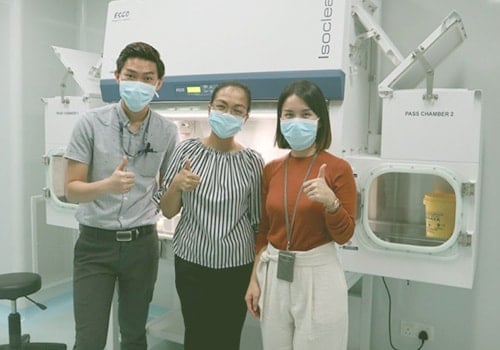
As support to clients, Esco offers process qualification to evaluate and collect data from the initial stages of process designing to production. This guarantees that an institution’s defined process will consistently delivery high quality products.
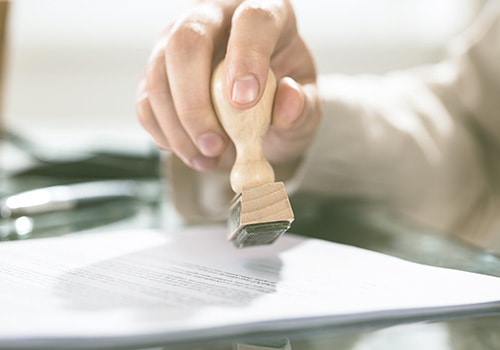
To consistently maintain safe operating conditions for any equipment, regular performance tests must be conducted. Esco’s Validation and Certification services assures all Esco equipment provide a sufficient working environment that is both pleasant and fully contained.
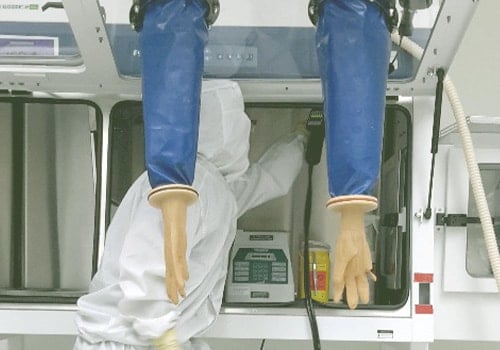
A schedule of planned service measures aimed for early detection of equipment issues to prevent unexpected process downtimes and failures.
Esco global services ensure compliance to legal guidelines and standards. We provide an uncomplicated validation of your system; from implementation to shut down.
Esco offers service programs to meet your individual needs, to ensure that your equipment is in excellent working condition.
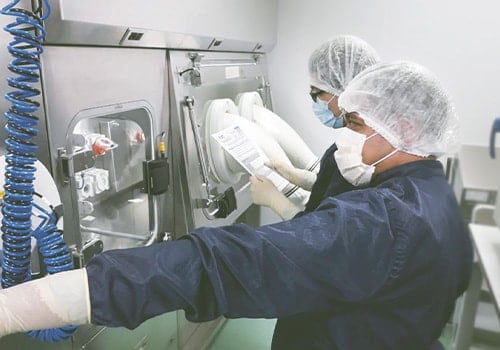
All equipment are manufactured as a commercial grade product. All replacement parts for consumables as well as any components that might fail while the product is in service will be provided by the company.
Each product is shipped with a Statement of Part Numbers for Replaceable Parts. There may be instances where Esco may use components from different sources; the serial number of that specific part (identification tag on its upper front side) may be used to inquire and retrieve the accurate part numbers.
Inquiries for equipment components may be directed to the respective Esco offices near you!
Check our corporate locations worldwide at www.escoglobal.com/corporate.php
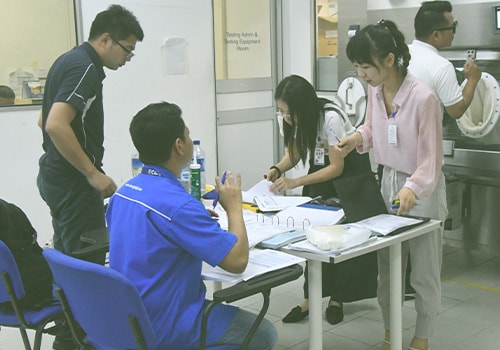
Esco offers user equipment trainings based on the procedures in the User and Service Manuals of each product.
Operational training includes product placement, electrical connection, connection to facility air handling system, adjustment of leveling feet and locking of casters, use of Sentinel Software and pressure measurement instrumentation, cleaning, decontamination, and filter changing technique.
Maintenance training includes the procedures used by our personnel described above.
Certification training is similar in scope to the training described above, and includes hands on demonstration of the skills being taught. Certified personnel assesses utilization, productivity, and risks of complicated or sensitive protocols. Those who complete Esco Certification Workshops will receive a certificate of attendance.
All of these are provided to guarantee that all operators are equipped and trained to properly use each Esco equipment.
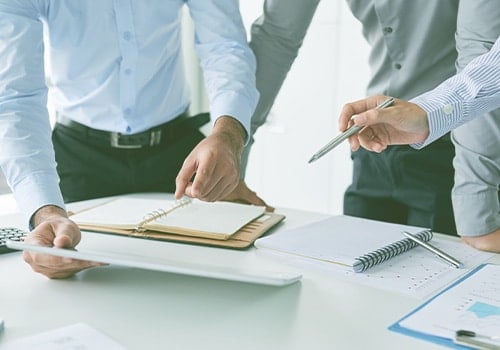
Our knowledgeable consultants are regularly sought to provide professional advise to numerous international regulating bodies on standard development, as well as, the re-evaluation of existing laboratory safety SOPs and manuals relevant to the industry.
Our knowledgeable consultants are regularly sought to provide professional advise to numerous international regulating bodies on standard development, as well as, the re-evaluation of existing laboratory safety SOPs and manuals relevant to the industry.
We are extremely qualified to provide professional advise to a wide array of projects such as: BSL2, BSL3, Biorisk Management, Biohazard Waste Management, Pre-Laboratory Certification Assessment, Good Laboratory Practice, Good Clinical Laboratory Practice, and Clean Room Design & Implementation. All these we do to ensure your productivity and product quality is maximized.
The wide range of spare parts carried in our factory headquarter include:
Replacement Filters
Safe change filter (Bag-In, Bag-Out) bags and rings
Replacement of sleeves and gloves
Gaskets
Beta transfers
Butterfly valves
Cooling coils
Magnehelic gauges