Streamline® Compounding Isolator (SCI)
Esco Healthcare’s Streamline® Compounding Isolator (SCI) provides a sterile environment for sterile/aseptic preparations and is designed in compliance with United States Pharmacopoeia (USP) General Chapter <797> for Pharmaceutical Compounding - Sterile Preparations and Hazardous Drugs - Handling in Healthcare Settings <800> criteria. It is factory-configured to operate either in a positive or negative pressure mode or with a recirculating or total exhaust airflow scheme.
This versatile isolator can be configured to be a compounding aseptic/sterile containment isolator (CACI) and compounding aseptic/sterile isolator (CAI),which is classified under Class 3 Leak Tight Containment as per ISO 10648-2.
Positive pressure is for sterile non-hazardous materials while negative pressure is for containment of sterile hazardous substances, ensuring product and operator safety.
Key Benefits:
-
Compliant to USP <797> and <800> guidelines
-
Class 3 pressure tested as per ISO 10648-2
-
ISO Class 5 air cleanliness as per ISO 14644-1
-
Fast purging time
-
Unidirectional airflow across the whole work zone at 0.40 m/s +/- 20%
-
Many pressure regime selections for product and operator safety
ULPA filters
(as per IEST-RP-CC001.3 and HEPA (H14) filter as per EN 1822) with a typical efficiency of >99.995% at 0.1 to 0.2 microns, providing ISO Class 3 air cleanliness as per ISO 14644-1.
- Bag-In, Bag-Out (BIBO) HEPA filter configuration (optional) offers additional protection for the maintenance personnel and environment by ensuring that upon filter changing, the HEPA filters are already sealed in a bag prior to being fully removed from the isolator unit.
FDA-grade pressure-tight static seals
Sentinel™ Gold microprocessor controller
supervises all functions and monitors airflow and pressure in real-time.
Robust dual-wall construction.
Unique Esco Dynamic Chamber™ plenum surrounds filter seals with negative pressure.
Safe-change cuff rings
permit hypalon sleeve changes with zero risk of work zone or environment contamination.
- Critical for operations dealing with potent (volatile) liquid or powder materials
- Guarantees operator and environmental protection is achieved as it prevents cross-contamination risk
Airlock pass-through interchange
ensures main work zone remains sterile during insertion and removal of items.
- Has electromagnetic interlocking door mechanism with time-delayed ingress/egress control.
The unit is equipped with a Foot Switch to open the inner doors.
Interchangeable Pressure Configuration
the work zone and pass-through interchange can be configured to have positive or negative pressurization.
- Positive pressure is for sterile non-hazardous materials.
- Negative pressure is for containment of sterile hazardous substances.
Stainless steel drain pan
located below the work surface to contain spills.
Hinged window
may be opened for thorough access into the work zone.
Sliding Tray
The pass-through chamber has a sliding tray for easy ingress of materials into the work zone.
Unit can be factory-configured
to have either a recirculating or total exhaust/single pass airflow scheme:
- Recirculating airflow can be applied for compounding non-hazardous sterile drugs.
- As per recommendations of USP <797> for compounding aseptic isolator (CAI) units.
- Total exhaust/single pass airflow is recommended for facilities handling volatile hazardous drugs
(HDs)/substances.
- Both USP <797> and <800> guidelines clearly define the use of a compounding aseptic containment isolator (CACI) for dealing with volatile HDs.
Recirculating Airflow
-
Ambient air is pulled through the inlet pre-filter and main filter located on top of the isolator.
-
The downflow filter creates a laminar air flow providing ISO Class 5 air cleanliness (ISO 14644-1) to the main chamber and pass-through, with a down flow velocity of 0.40 m/s +/- 20%.
-
Air from the work zone and pass-through is quickly purged out by the exhaust fan to keep the area clean. The fan pulls approximately 70% of the purged air back to the plenum, passes through the HEPA downflow filter again, and is recirculated back to the work zone and pass-through.
-
Approximately 30% of the purged air is exhausted through the filter to prevent heat build-up inside the isolator.
-
Exhausted air is replenished by ambient air coming from the top inlet prefilter that has 80% efficiency.
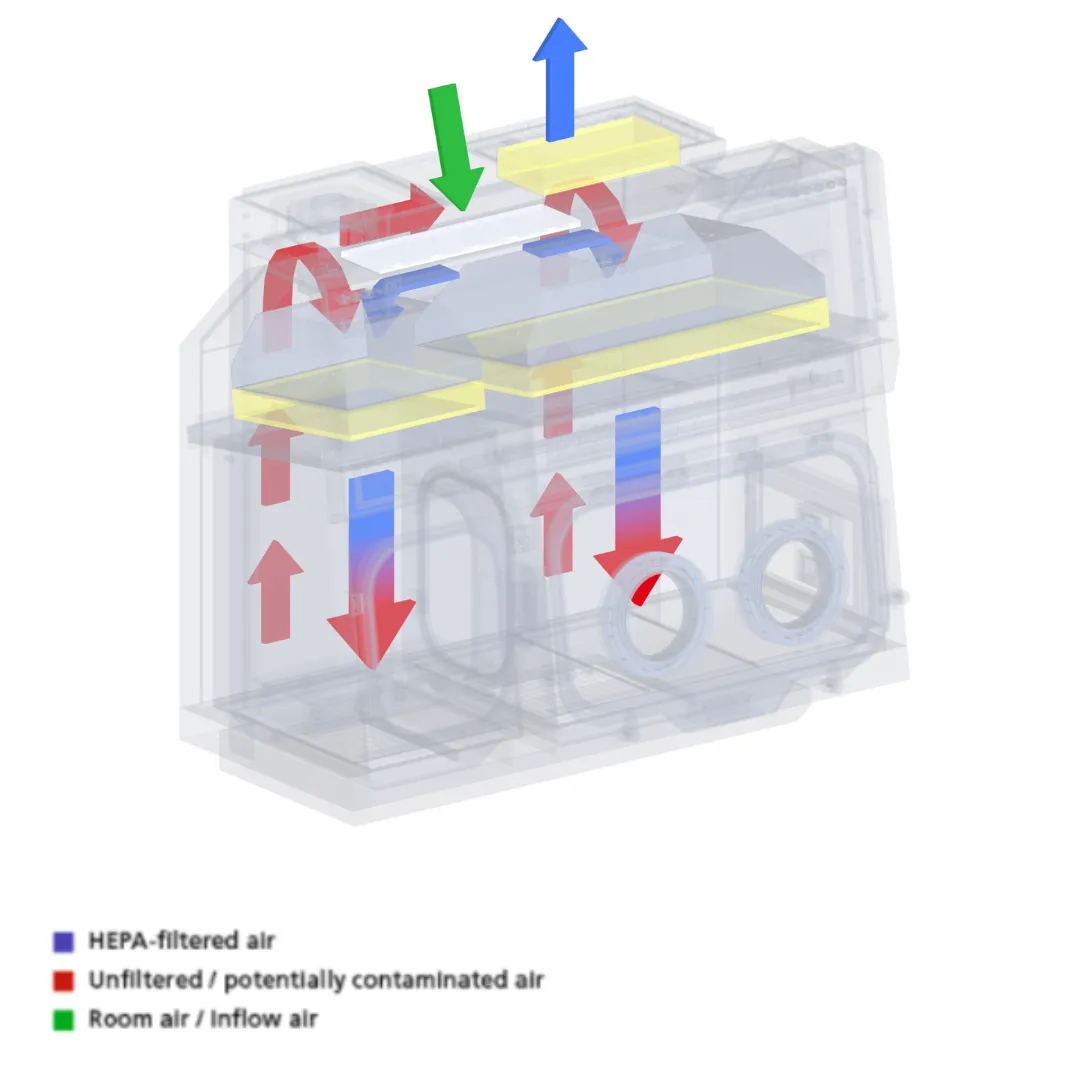
Total Exhaust
-
Ambient air is pulled through the inlet pre and main filter via the main fans at the top of the isolator. This creates positive pressure on the plenum which provides the downflow of air with a velocity of 0.40 m/s ± 20%.
-
The pre-filter extends the life of the filters by trapping larger particulates that can easily clog the main filters
-
-
This downflow supply then provides an ISO Class 5 environment and unidirectional airflow inside the isolator; thus, protecting the materials inside the main chamber and pass-through.
-
Air from the work zone and pass-through is then quickly purged by the fans to keep the area clean. The purge is completely exhausted through HEPA filters as well; ensuring that only clean air is exhausted back to the environment.
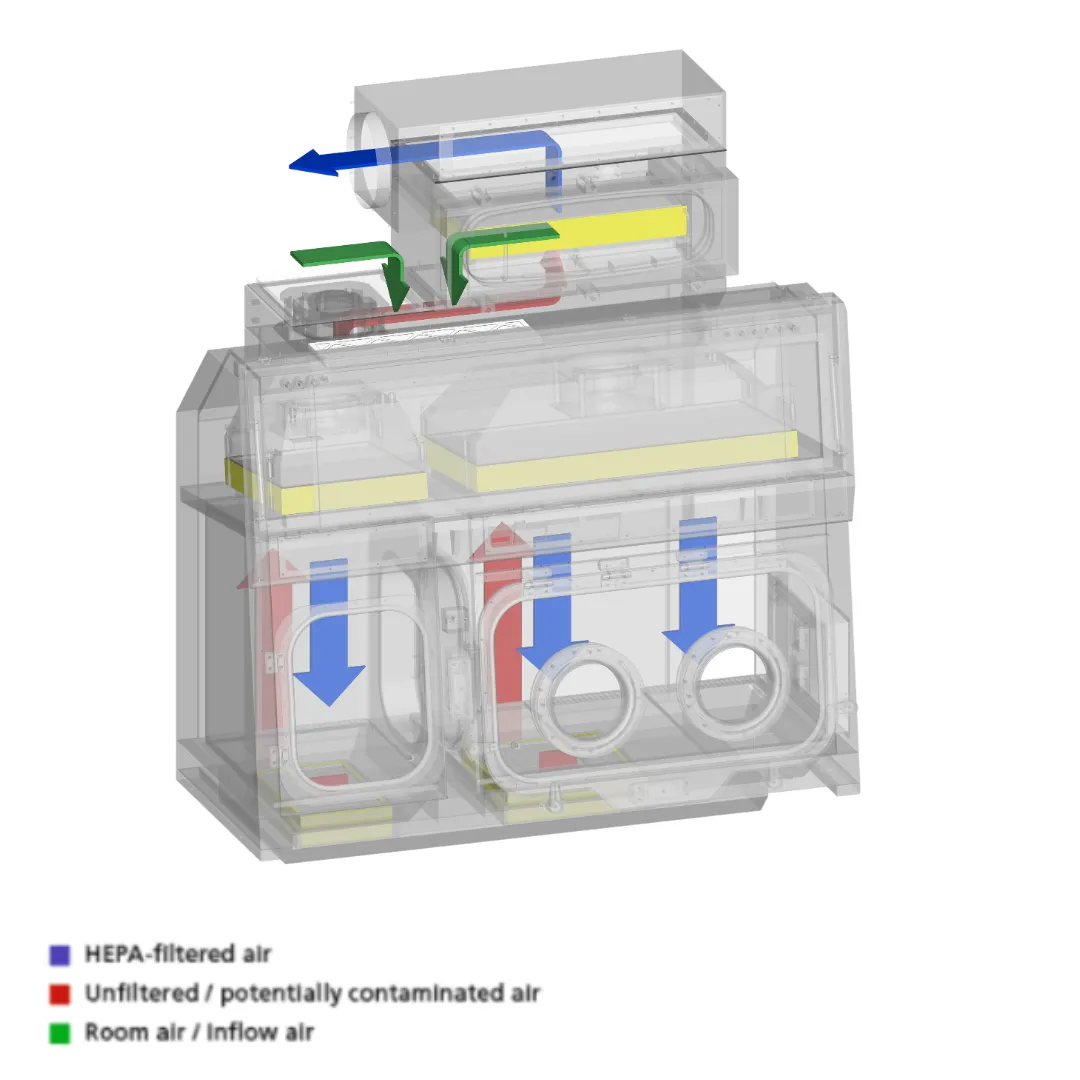
Upon ordering, input material of construction at the end of the model code: SCI-2G_-N1RL-1-SE-SS or -EG
-
SS: Full stainless steel exterior
-
EG: Electrogalvanized steel with ISOCIDE™ coating
*The configuration allows for 1 sharps container and 1 stainless steel vessel for other laboratory waste
Note:
- No difference of height for the unit with and without sharps bin disposal below the work zone
- To add ABBV, please add +420mm for the overall height
- For Exhaust Type-2, to add an Exhaust Carbon Filter, please add +65 mm for the overall height
- For Exhaust Type-2, to add Exhaust Collar, please add +105mm for the overall height
- For Exhaust Type-1 and 3, to add the Top Exhaust collar with/without the Exhaust Carbon Filter, please add +205mm for the overall height
- For Exhaust Type-1 and 3, to add the Side Exhaust collar with/without Exhaust Carbon Filter, please add +165mm for the overall height
- For Exhaust Type-1 and 3, the standard base unit will need to be connected to ducting.
Standard Accessories
-
Electromagnetic interlocking doors to prevent cross-contamination
Foot switch included to easily open the inner doors
Single piece stainless steel 316L work top for SCI-Gen 2 with sharp bin container below the work zone (-SB)
Multiple piece stainless steel 316L work top for SCI-Gen 2 without sharp bin container (-0)
Energy efficient LED lighting with higher durability and better quality
Electrical Outlets and Utility Fittings
Electrical outlet, ground fault, North America
Electrical outlet, Euro/Worldwide
Support Stands
Fixed height, available 711 mm (28") or 864 mm (34") - With leveling feet, ± 38.1 mm (1.5") (SAL) - With casters (SPC)
Telescoping height stand for leveling feet (STL), nominal range 660 mm to 960 mm (26"to 37.8")
Telescoping height stand for casters (STC), nominal range 660 mm to 880 mm (26" to 34.6") - Adjustable in 25.4 mm (1") increments
Infinitely adjustable hydraulic stand with casters elevates to accommodate a sitting or a standing user’s work surface height (SHM)
-
External material of construction:
Electrogalvanized steel with ISOCIDE™ powder coating
Stainless steel 304
-
Exhaust types
Double HEPA exhaust filter (BIBO top and non-BIBO bottom)
Side Exhaust Connection (for TE units)
*Note: Additional carbon filter is available as an option for all exhaust filter configurations
IV bar, with hooks
UV lamp
Top or side exhaust collar
Anti-blowback valve
Perforated shelf to increase work zone space
Alarm package
Laboratory cart
Adjustable foot rest
Stainless steel turntable
Manual latches
Granite slab
Damper
-
Sharp bin container
Bottom of the work zone
Beside the work zone
Add-Ons
Monitor System
Mounted on the rear of the isolator
Beside the front panel; equipped with a keyboard and mouse arm
Glove Leak Tester
-
Automated pressure hold testing (APHT)
With on-board compressed air
with on-board pump
-
CCTV integration
Side panel with stainless steel mount
Rear wall of the work zone
Back-up battery for the electromagnetic interlocks (contact Esco for more information)