Blow-Fill-Seal Technology and Isolators
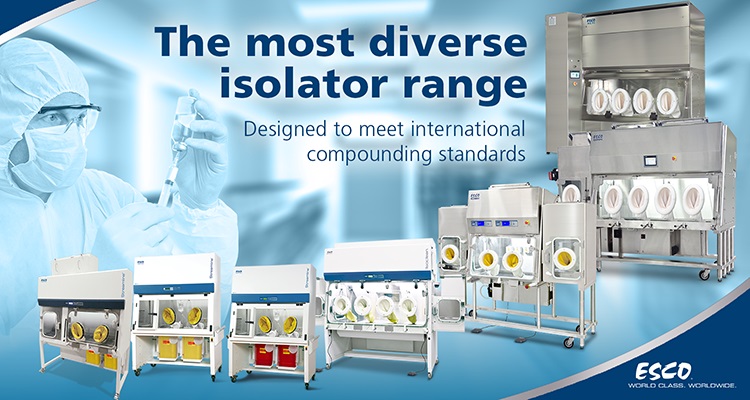
Microbial contamination is one severe concern for pharmaceutical companies manufacturing liquid formulations, which serves as desirable growth areas for various types of microorganisms. Sterile preparations that are contaminated may cause drug deterioration, and even toxic reactions. Hence, any form of microbial contamination is hazardous.
Blow-fill-seal (BFS) aseptic processing is an advanced technology perceived to be a proficient and safe system in filling and packaging sterile pharmaceutical liquids and other related health products used in ophthalmic and respiratory condition management. It allows container to be formed from plastic, aseptically-filled and hermetically-sealed in an uninterrupted, assimilated and spontaneous operation.
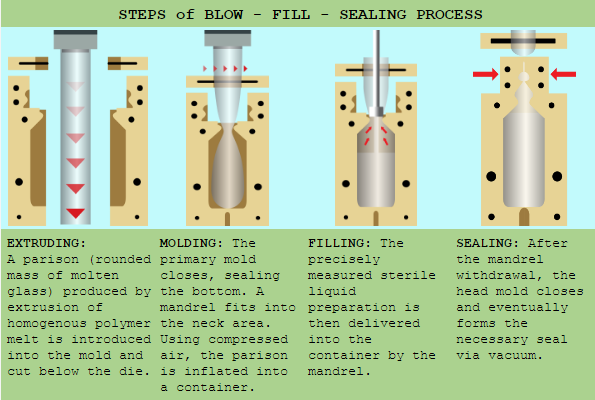
The BFS manufacturing technique is used to produce small, (0.1mL) and large volume, (500mL +) liquid-filled containers. It is considered to be the superior form of aseptic processing by various medicine regulatory agencies including the U.S. Food and Drug Administration (FDA) in the packaging of pharmaceutical and healthcare products.
Isolators modified for B/F/S enclosure applications provide a higher level of sterility assurance for liquid preparations with plastic metered-dose containers and rubber/silicone stoppers via Class 100 environment.
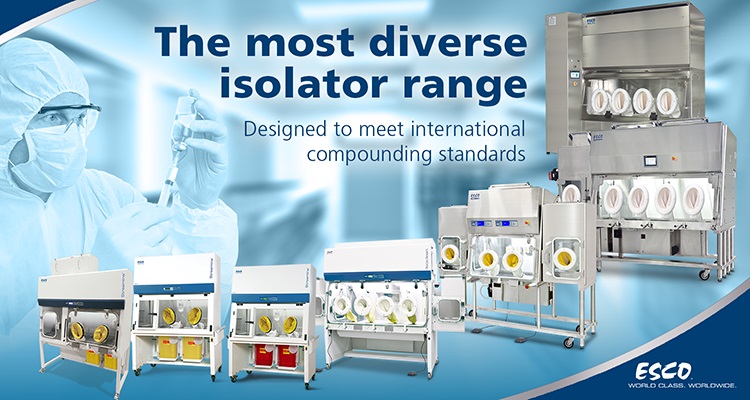
The control of air quality is a serious consideration in the manufacturing of sterile drug products. Esco’s isolators are designed for particular measures to decrease microbial contamination as well as particle levels that can contaminate the exposed product.
Esco Pharma offers a wide-range of modular isolators that will meet and satisfy your specific needs.