Aseptic Containment Isolator (ACTI)
Esco Aseptic Containment Isolator (ACTI) works in conjunction with advanced material transfer techniques and a biodecontamination system which provides a 6 log reduction in viable contaminants.
ACTI provides standard configurable designs able to adapt to various batch sizes and process flows. Through a user-friendly operating system, this isolator can be setup to operate under recirculating or total exhaust airflow scheme and in positive or negative pressure mode. This allows the system to be multifunctional and caters all of the requirements for both toxic and non-toxic aseptic materials.
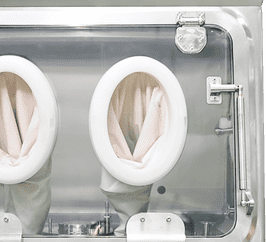
-
Unidirectional airflow – 0.45m/s ± 20% measured 150mm from the distribution screen face during normal operation provides ISO 5 / Grade A aseptic environment.
Knife edge gel sealed U15 supply and optional U15 return filters
Gasket sealed F8 room inlet and outlet filters
System automatically compensates for containment breach in +ve or -ve mode via an egress or inward rush respectively
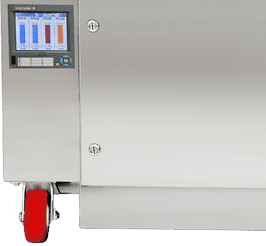
Optional VHP Ports for automated aseptic processing allowing chamber or system decontamination.
Biodecontamination loop for decontamination of viable or non viable monitoring systems
Optional humidity/temperature sensors for environmental monitoring
External sensors protected by instrument filters
Optional distribution manifold allows more accurate sampling of upstream filter PAO concentration (since this manifold draws in PAO it is advice that this be cleaned before every filter change).
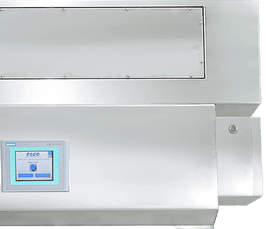
Filter scanning ports for downstream filter integrity testing.
Automated raise/lower carriage system via user ID input allows isolator to be raised to operator defined ergonomic height
Safe change gloveport assembly allows for either single piece or split cuff gloves to be change without any breach in isolator condition
Enhanced uniformity and entrainment of powders via our PLF screens
-
Smooth flushed interior of isolator glazing means less crevices to improve cleanability / decontamination
Single piece chamber fabricated of SS 316L hand polished to less than 0.4 microns with 19mm coved corners
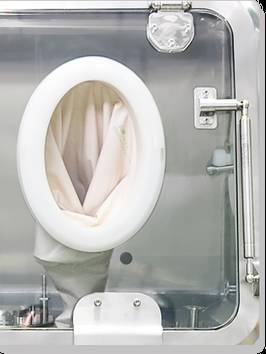
Glazing is made of toughened laminated safety glass
PLF diffuser screens provides uniform airflow throughout the interior work zone
Stainless steel is passivated post-fabrication with citric acid
Clean sanitary finishing and perforated multi-piece work tray enhances unidirectional airflow for ultimate entrainment of contaminants and of potent powders
International brand safe change filters means lower replacement costs and quicker turn-around time
HMI/PLC control architecture with 4 defined levels of hierarchy
Access for common replaceable items such as lights and ballasts are done all from the front of the unit
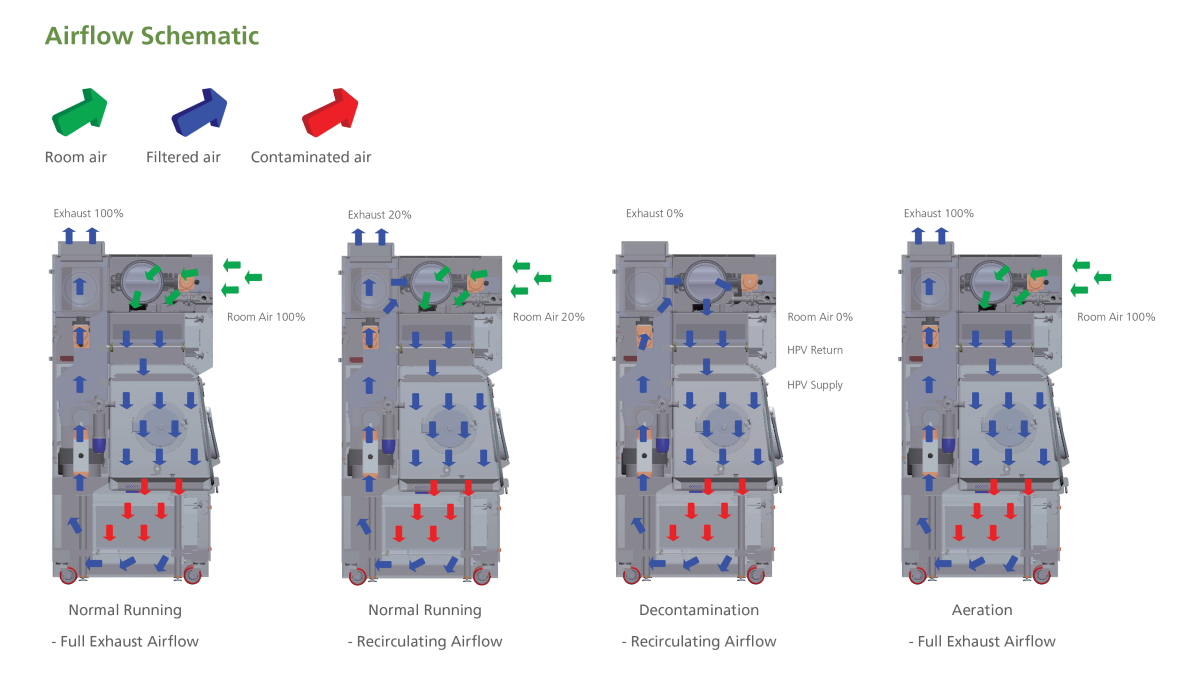
Total unidirectional airflow provides superior aseptic work zones.
Safety toughened laminated glass hinges upwards assisted with gas springs for batch loading.
-
Airflow regime either runs in recirculatory or total exhaust airflow.
Total exhaust airflow for fast purging of biodecontamination agent during aeration period.
Recirculation option for reduced airflow taken from the room, thus, less air is exhausted during normal operation and during conditioning and decontamination phases.
-
U15 supply and exhaust filters suitable for either toxic or non-toxic aseptic materials.
Exhaust filter is directly below the isolator and can be removed with a bypass tube fitted (for non-potent material applications)
GENERAL SPECIFICATIONS Aseptic Containment Isolator (ACTI) |
ACTI-2G_ |
ACTI-3G_ |
ACTI-4G_ |
|
Main Chamber Nominal Size |
1200 mm (47.2”) |
1500 mm (59.1”) |
1900 mm (74.8”) |
|
Working Chamber Dimensions (W x D x H) |
1200 x 670 x 796 mm (47.2” x 26.4” x 31.3”) |
1500 x 670 x 796 mm (59.1” x 26.4” x 31.3”) |
1900 x 670 x 796 mm (74.8” x 26.4” x 31.3”) |
|
External Dimensions (W x D x H) |
2100 x 1007 x 2502 mm (82.7” x 39.6” x 98.5”) |
2400 x 1007 x 2502 mm (94.5” 39.6” x 98.5”) |
2800 x 1007 x 2502 mm (110.2” 39.6” x 98.5”) |
|
Chamber Environment |
ISO Class 5 all Chambers (Grade A) |
|||
Filter Type – Isolator Inlet |
ULPA U15 with integral mesh guard and knife edge gel seal |
|||
Filter Efficiency – Inlet |
99.9995% at MPPS |
99.9995% at MPPS |
99.9995% at MPPS |
|
Filter Type – Isolator Exhaust |
HEPA H14 with knife edge gel seal |
|||
Filter Efficiency – Exhaust |
99.995% at MPPS |
99.995% at MPPS |
99.995% at MPPS |
|
Lighting Level |
≥ 600 lux (≥ 56 foot-candles) |
≥ 600 lux (≥ 56 foot-candles) |
≥ 600 lux (≥ 56 foot-candles) |
|
Sound Level |
≤ 68 dBA |
≤ 68 dBA |
≤ 68 dBA |
|
Isolator Construction |
Chamber |
316L |
316L |
316L |
Service Housing |
316L |
316L |
316L |
|
Support Frame |
316L |
316L |
316L |
|
Isolator Finish |
Chamber Internal |
≤0.4 Ra |
≤0.4 Ra |
≤0.4 Ra |
Chamber External |
≤0.6 Ra |
≤0.6 Ra |
≤0.6 Ra |
|
Service Housing External |
0.6 Ra |
0.6 Ra |
0.6 Ra |
|
Support Frame |
1.0 Ra |
1.0 Ra |
1.0 Ra |
|
Electrical Requirements |
220-240V, AC, 50Hz, 1Ø |
✓ |
✓ |
✓ |
110-120V, AC, 60Hz, 1Ø |
✓ |
✓ |
✓ |
|
220-240V, AC, 60Hz, 1Ø |
✓ |
✓ |
✓ |
|
Compressed Air requirements |
6 Barg Pressure at 5ltr/sec |
✓ |
✓ |
✓ |
Exhaust Duct Requirements |
10” Duct from Isolator to Outside |
|||
Options |
Pass Chamber |
✓ |
✓ |
✓ |
Bio-decontamination – BioVap™ |
✓ |
✓ |
✓ |
|
Non-Viable Air Sampler |
✓ |
✓ |
✓ |
|
Viable Air Sampler |
✓ |
✓ |
✓ |
|
Sterility Test Pump |
✓ |
✓ |
✓ |
|
Glove Tester |
✓ |
✓ |
✓ |
|
Waste Bag Grommet |
✓ |
✓ |
✓ |
|
Sterile Continuous Liner |
✓ |
✓ |
✓ |
|
Bag-Welder with Table |
✓ |
✓ |
✓ |
|
RTP Ø270 – Alpha |
✓ |
✓ |
✓ |
|
RTP Ø270 – Beta Canister |
✓ |
✓ |
✓ |
|
RTP Ø270 – Beta Liner |
✓ |
✓ |
✓ |
BUILT-IN OPTIONS
-
Integrated automated pressure testing
-
Filters can be upgraded to safe change with additional bags - Bag-In, Bag-Out (BIBO) rings
-
Bypass option can be retrofitted with additional safe change housing
-
System runs in any of the following airflow regimes in both positive and negative and can be configured in-situ by administrator access
-
Volt free contacts provided for client connection to HVAC and optional 21 CFR Part 11 chart recorder for storing of process data