Containment Barrier Isolator - Turbulent (CBI-T)
Your Practical Solution to cGMP Compliance
Esco Healthcare’s Containment Barrier Isolator – Turbulent Model (CBI-T) is designed to provide isolation of the product or process involving potent powder compounds. It operates in a turbulent airflow regime and facilitates the required environment for powder handling processes like weighing and dispensing.
As a containment isolator, the CBI-T operates in a negative pressure mode and provides filtered air into the work chamber. It facilitates the mixing and dilution of airborne contaminants, thus reducing the concentration within the environment. Air from the work chamber is then exhausted through the exhaust filter system.
The CBI-T can be integrated with weighing balances mounted on an anti-vibration slab to facilitate the accurate weighing and dispensing of powders.
Applications:
- Potent Powder Handling
- Weighing and Dispensing of Powders
- Highly Potent Active Pharmaceutical Ingredients (HPAPIs) QC Testing
- Powder Containment
- Research and Development
- Pharmaceutical Manufacturing
Full Stainless Steel Construction
Fully welded Stainless steel 316L internal chambers with Stainless steel 304 external housing
HMI/PLC Control System
Supervises and controls all functions of the unit and monitors operating parameters
Emergency Control
Emergency Stop (E-stop) button located in the front panel of the unit for easy access
Safe Change H14 Filter Design
Designed with Push-Push Filters for easy and safe filter replacement
Easy-to-clean Work Chamber
Designed with no coves, corners, and crevices for easy cleaning
Cleaning Equipment Integration
Can be designed and integrated with CIP/WIP equipment for the most demanding cleaning operations of powder handling
Cost-effective Solution for Potent Powder Handling
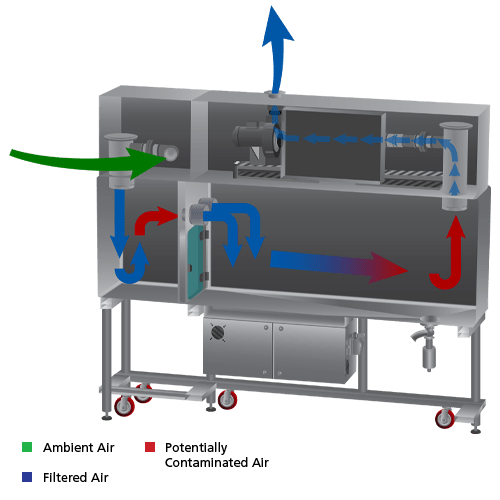
During the operation of the Containment Barrier Isolator – Turbulent (CBI-T), ambient air is pulled through the inlet pre-filter in front of the isolator. The air then is pulled towards the push-push filter to the passthrough chamber. When the air enters the passthrough chamber, it creates a turbulent flow. From the passthrough chamber, the air is then pulled towards the push-push filter and transfers to the main chamber of the isolator unit. This filtered air also creates a turbulent flow in the main chamber. This process repeats over and over to maintain the low concentration of contaminants within the work area. Air is then exhausted out from the top portion of the isolator after passing through another stage of filtration.
GENERAL SPECIFICATIONS Containment Barrier Isolator - Turbulent |
CBI-T-2G |
CBI-T-3G |
CBI-T-4G |
|
Main Chamber Nominal Size (mm) |
1.2 meter (4’) |
1.6 meter (5.2’) |
2.00 meter (6.6’) |
|
Process Chamber External Dimension - (W x D x H) |
1.20 m x 0.64 m x 0.84 m (4’ x 2.1’ x 2.8’) |
1.60 m x 0.64 m x 0.84 m (5.2’ x 2.1 x 2.8’) |
2.0 m x 0.64 m x 0.84 (6.6’ x 2.1’ x 2.8’) |
|
Pass-through Chamber External Dimension - (W x D x H) |
0.6 m x 0.52 m x 0.84 m (2’ x 1.7’ x 2.8’) |
|||
External Dimensions with 1 Pass Chamber - (W x D x H) |
1.83 m x 0.70 m x 2.28 m (6’ x 2.3’ x 7.5’) |
2.23 m x 0.70 m x 2.28 m (7.3’ x 2.3’ x 7.5’) |
2.63 m x 0.70 x 2.28 m (8.6’ x 2.3’ x 7.5’) |
|
Glove Port Diameter (mm) |
200 mm x 300 mm |
|||
Glove Port Quantity |
2 |
3 |
4 |
|
Chamber Pressure |
Negative Pressure |
|||
Airflow Type |
Turbulent Flow |
|||
Chamber Environment |
ISO Class 8 (Grade D) |
|||
Filter Type - Inlet |
HEPA (H14) Cartridge Filter |
|||
Filter Efficiency - Inlet |
99.98% |
|||
Filter Type - Exhaust |
HEPA (H14) Cartridge Filter |
|||
Filter Efficiency - Exhaust |
99.98% |
|||
Lighting Level |
>650 Lux |
|||
Sound Level |
≤ 80 dBA |
|||
Air Change Per Hour |
Process Chamber |
48 |
36 |
29 |
Pass Chamber |
61 |
61 |
61 |
|
Air Volume (m3/h) |
Process Chamber |
31 |
31 |
31 |
Pass Chamber |
16 |
16 |
16 |
|
Isolator Construction |
Main Body |
SS 316L |
||
Internal Chambers |
SS 316L |
|||
Support Frame and Service Housing |
SS 304 |
|||
Electrical Requirements (by Client) |
230 VAC, |
CBI-T-2G8 |
CBI-T-3G8 |
CBI-T-4G8 |
110-120 VAC, |
CBI-T-2G9 |
CBI-T-3G9 |
CBI-T-4G9 |
|
Compressed Air Requirement (by Client) |
2 Bar-g Pressure at 5 L/sec |
2 Bar |
||
Exhaust Duct requirements (by Client) |
4” (101.6mm) |
|||
Net Weight |
TBD |
TBD |
TBD |
|
Shipping Weight |
TBD |
TBD |
TBD |
|
Shipping Dimension (W x D x H) |
TBD |
TBD |
TBD |
|
Shipping Volume (Maximum) |
TBD |
TBD |
TBD |
LIST OF OPTIONS for CBI Models | CBI-U | CBI - T | CBI-III | CBI-H | |||
4" Split Butterfly Valve (for powder discharge of powder below isolator chamber) | ✔ | ✔ | |||||
Adjustable Hydraulic Stand (based on operator ID input) | ✔ | ✔ | ✔ | ||||
Exhaust Box (with automated dampers with inflatable seals or manual with valve) | ✔ | ✔ | ✔ | ||||
Anti-blow back damper box | ✔ | ✔ | ✔ | ||||
Automated Pressure Hold Test | with Client Supplied Compressed Air | ✔ | ✔ | ✔ | ✔ | ||
with On-board Air Compressor | ✔ | ✔ | ✔ | ✔ | |||
Bag Welder with Table Bag-out Port |
✔ | ✔ | ✔ | ||||
Bio Dunk Tank Bag Out Port |
✔ | ✔ | |||||
Mobile Biodecontamination BioVap TM | ✔ | ✔ | ✔ | ||||
Carbon Filter | ✔ | ||||||
Convertible to Class 1 cabinet | ✔ | ||||||
Integration of small scale aseptic or potent tablet/capsule etc… | ✔ | ✔ | ✔ | ✔ | |||
Double-sided access | ✔ | ✔ | ✔ | ||||
Manual Drain Ball Valve (for client controlled CIP/WP) must order with inner pass-through inflatable sealed doors. | ✔ | ✔ | |||||
Electrical Outlet (IP66) | IP 66 | ✔ | ✔ | ✔ | ✔ | ||
ATEX Zone 1/21 (only for internal environment) | ✔ | ✔ | ✔ | ||||
ATEX rating up to zone 1/21 internally only (ATEX fan, “IS” signals for internal door sensor/push button) | ✔ | ✔ | |||||
Glove Leak Tester | ✔ | ✔ | ✔ | ✔ | |||
Formalin Vaporizer (auto neutralization and purge cycle) | ✔ | ✔ | ✔ | ||||
H2O2 Monitoring (sensor is not integrated with HMI) | ✔ | ✔ | ✔ | ||||
Liquid Water Entry / Exit Ports | ✔ | ✔ | |||||
N2 Purge for Process Chamber | ✔ | ||||||
Ø250 mm Product Waste Bag Out Ports / | ✔ | ||||||
Battery option to maintain EM interlock during power outage or E Stop | ✔ | ✔ | ✔ | ✔ | |||
Particle Counter | Portable Paricle Counter (Non-viable) | ✔ | ✔ | ✔ | |||
Microbial Air Samples (Viable Particle Counter) | ✔ | ✔ | ✔ | ||||
Product Waste Entry / Exit Ports | ✔ | ✔ | |||||
RTPØ 105, 190, 270 - Alpha | ✔ | ✔ | ✔ | ✔ | |||
RTPØ 105, 190, 270 - Beta Canister | ✔ | ✔ | |||||
RTPØ 105, 190, 270 - Beta Liner | ✔ | ✔ | |||||
RTPØ 350, 460 - Alpha, Beta Liner, Beta Canister | ✔ | ✔ | ✔ | ||||
Service Fixtures (Vacuum, Nitrogen, Compressed Air, Nozzle for BioVap) | ✔ | ✔ | ✔ | ✔ | |||
Spray Ball (CIP) with Manual Ball Valve | ✔ | ||||||
Spray Gun (WIP) with Manual Ball Valve | ✔ | ✔ | |||||
Sterile Continuous Liner | ✔ | ✔ | ✔ | ||||
Sterility Test Pump | ✔ | ||||||
Temperature and Relative Humidity Monitoring (only for process chamber) | ✔ | ✔ | ✔ | ✔ | |||
Rear view monitor | ✔ | ✔ | ✔ | ✔ | |||
UV Lamp | ✔ | ✔ | |||||
Weighing Scale Granite Slab | ✔ | ✔ | ✔ | ||||
Sharps (inside) | ✔ |
What are the common sets of equipment to be integrated with a CBI-T Unit?
As a powder containment isolator, common equipment to be integrated are weighing balances, CIP/WIP system (e.g., spray gun, spray ball), and Rapid-transfer ports (RTPs).
How is the cleaning process done in this unit?
The cleaning process is commonly done through the use of spray guns or spray balls. If these systems are not integrated, the cleaning can be carried out manually.
Can a VHP system like the BioVap™ be integrated into the unit?
No, VHP systems are usually not needed in powder handling applications.
What are the sizes available for this unit?
Standard CBI-T model is available in 2-glove, 3-glove, and 4-glove sizes with the option to integrate 1 or 2 passthrough chambers.
What is the difference between CBI-T and WDCI?
Though both are intended for powder weighing applications, CBI-T is the more affordable solution as compared to the WDCI. However, it only comes in a standard size and offers fewer customization capabilities.