Containment Barrier Isolator (CBI) - Undirectional
Your Practical Solution to cGMP Compliance
Containment Barrier Isolator - Unidirectional (CBI-U) utilizes unidirectional/laminar airflow and facilitates the isolation of a product or process while providing the required conditions (ISO Class 5/ Grade A Environment) for a sterile/aseptic environment. This equipment provides a comprehensive range of personnel, product, and environmental protection.
It is factory-configured to operate at positive or negative pressure in single pass or recirculating airflow. The type of application dictates the operating parameters (pressure/airflow) of the CBI-U.
Applications:
Pharmacy Compounding (Chemotherapy/TPN)
Small-Scale Potent Material Handling
Aseptic Processing
Sterility Testing
Research and Development
Cell Processing
- Laminar / Unidirectional airflow that complies to standards for sterile product handling
HEPA (H14) filters with a typical efficiency of > 99.999% at 0.3 microns provide superior ISO Class 5 air cleanliness (Grade A)
Recovery Time to maintain ISO Class 5 environment is less than 60 seconds
Class II Containment as per ISO 10648-2 leak tightness
Type D Passthrough Chambers equipped with electromagnetic interlocking mechanism and time-delay effect
Safe glove change and low contamination filter change
FDA-grade static seals
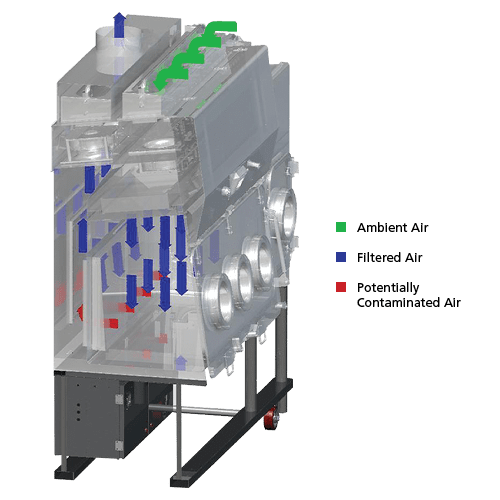
Ambient air is pulled through the inlet prefilter located on top of the isolator. Air from the top inlet and from work zone is pulled by the fan which creates a positive pressure on the plenum that creates downflow. The HEPA (H14) downflow filter creates a laminar and particle-free ISO Class 5 air cleanliness as per ISO 14644-1 (equivalent to Class 100 as per US Fed Std 209E) inside the isolator to protect the work material inside the main chamber and pass-thru. Air fromthe work zone and pass-thru is quickly purged out by the fan to keep the area clean. The fan pulls approximately 90% of the purged air back to the plenum and after passing through the HEPA (H14) downflow filter.
The high rate of airflow recirculation helps to prolong filter life and reduces the chances of ambient contaminants entering the work zone. For a recirculating model, approximately 10% of the purged air is exhausted through an HEPA-filter to prevent heat build-up inside the isolator that can be detrimental to drug compounding. This exhausted air is replenished by ambient air coming from the top inlet prefilter and a filter with 80% efficiency for positive pressure model. For a Total Exhaust/Single-Pass Model, 100% of the air is exhausted out of the isolator.
GENERAL SPECIFICATIONS Containment Barrier Isolator - Unidirectional |
CBI-U-2G |
CBI-U-3G |
CBI-U-4G |
|
Main Chamber Nominal Size (Width) |
1.2 meter (4’) |
1.6 meter (5.2’) |
2.0 m (6.6’) |
|
Working Chamber Dimensions - Min (W x D x H) |
1.2 m x 0.550 m x 0.77 m |
1.6 m x 0.55 m x 0.77 m |
2.0 m x 0.55 m x 0.77 |
|
Working Chamber Dimensions - Max (W x D x H) |
1.2 m x 0.626 m x 0.84 m |
1.6 m x 0.626 m x 0.84 m |
2.0 m x 0.626 m x 0.84 m |
|
External Dimension |
With Adjustable Base Stand (Min) |
1.815 m x 0.92 m x 2.26 m |
2.215 m x 0.92 m x 2.26 m |
2.615 m x 0.92 m x 2.26 m |
With Adjustable Base Stand (Max) |
1.815 m x 0.92 m x 2.56 m |
2.22 m x 0.92 m x 2.56 m |
2.615 m x 0.92 m x 2.56 m |
|
Glove Port Height (Min) |
1000 mm |
1000 mm |
1000 mm |
|
Glove Port Height (Max) |
1300 mm |
1300 mm |
1300 mm |
|
Chamber Environment |
ISO Class 5 all chambers (Grade A) |
|||
Chamber Pressure |
Factory-Configured Either Positive or Negative Pressure |
|||
Airflow Type |
Unidirectional/ Laminar Airflow |
|||
Filter Type - Chamber Inlet |
HEPA (H14) Filter with Integral Mesh Guard and Gasket Seal |
|||
Filter Efficiency - Chamber Inlet |
99.995% |
|||
Filter Type - Chamber Exhaust |
HEPA (H14) Filter with Integral Mesh Guard and Gasket Seal |
|||
Filter Efficiency - Chamber Exhaust |
99.995% |
|||
Lighting Level |
≥ 500 Lux (6000 K) |
|||
Sound Level |
≤ 80 dBA |
|||
Isolator Construction |
Chamber |
SS 316L |
||
Service Housing |
SS 304 |
|||
Support Frame |
SS 304 |
|||
Isolator Finish |
Chamber Internal |
≤ 0.4 Ra |
||
Chamber External |
≤ 0.6 Ra |
|||
Serivce Housing External |
≤ 0.6 Ra |
|||
Support Frame |
≤ 1.0 Ra |
|||
Electrical Requirements |
220-240 VAC, |
CBI-U-2G8 |
CBI-U-3G8 |
CBI-U-4G8 |
(by Client) |
110-120 VAC, |
CBI-U-2G9 |
CBI-U-3G9 |
CBI-U-4G9 |
Compressed Air Requirement (by Client) |
2 Bar-g Pressure at 5 L/sec |
✔ |
✔ |
✔ |
Exhaust Duct Requirements (by Client) |
10” Duct from Isolator to Outside |
|||
Estimated Weight of Cabinet (1 PTC) |
721 kg |
900 kg |
1121 kg |
|
Estimated Weight of Cabinet (2 PTC) |
851 kg |
1030 kg |
1209 kg |
|
Net Weight |
929 kg |
1260 kg |
||
Shipping Weight |
979 kg |
1320 kg |
||
Shipping Dimension (W x D x H) |
1550 X 950 X 1760 mm |
2500 X 1080 X 2400 mm |
3370 X 1100 X 2420 mm |
|
Shipping Volume (Maximum) |
2.59 |
6.48 |
8.97 |
LIST OF OPTIONS for CBI Models | CBI-U | CBI - T | CBI-III | CBI-H | |||
4" Split Butterfly Valve (for powder discharge of powder below isolator chamber) | ✔ | ✔ | |||||
Adjustable Hydraulic Stand (based on operator ID input) | ✔ | ✔ | ✔ | ||||
Exhaust Box (with automated dampers with inflatable seals or manual with valve) | ✔ | ✔ | ✔ | ||||
Anti-blow back damper box | ✔ | ✔ | ✔ | ||||
Automated Pressure Hold Test | with Client Supplied Compressed Air | ✔ | ✔ | ✔ | ✔ | ||
with On-board Air Compressor | ✔ | ✔ | ✔ | ✔ | |||
Bag Welder with Table Bag-out Port |
✔ | ✔ | ✔ | ||||
Bio Dunk Tank Bag Out Port |
✔ | ✔ | |||||
Mobile Biodecontamination BioVap TM | ✔ | ✔ | ✔ | ||||
Carbon Filter | ✔ | ||||||
Convertible to Class 1 cabinet | ✔ | ||||||
Integration of small scale aseptic or potent tablet/capsule etc… | ✔ | ✔ | ✔ | ✔ | |||
Double-sided access | ✔ | ✔ | ✔ | ||||
Manual Drain Ball Valve (for client controlled CIP/WP) must order with inner pass-through inflatable sealed doors. | ✔ | ✔ | |||||
Electrical Outlet (IP66) | IP 66 | ✔ | ✔ | ✔ | ✔ | ||
ATEX Zone 1/21 (only for internal environment) | ✔ | ✔ | ✔ | ||||
ATEX rating up to zone 1/21 internally only (ATEX fan, “IS” signals for internal door sensor/push button) | ✔ | ✔ | |||||
Glove Leak Tester | ✔ | ✔ | ✔ | ✔ | |||
Formalin Vaporizer (auto neutralization and purge cycle) | ✔ | ✔ | ✔ | ||||
H2O2 Monitoring (sensor is not integrated with HMI) | ✔ | ✔ | ✔ | ||||
Liquid Water Entry / Exit Ports | ✔ | ✔ | |||||
N2 Purge for Process Chamber | ✔ | ||||||
Ø250 mm Product Waste Bag Out Ports / | ✔ | ||||||
Battery option to maintain EM interlock during power outage or E Stop | ✔ | ✔ | ✔ | ✔ | |||
Particle Counter | Portable Paricle Counter (Non-viable) | ✔ | ✔ | ✔ | |||
Microbial Air Samples (Viable Particle Counter) | ✔ | ✔ | ✔ | ||||
Product Waste Entry / Exit Ports | ✔ | ✔ | |||||
RTPØ 105, 190, 270 - Alpha | ✔ | ✔ | ✔ | ✔ | |||
RTPØ 105, 190, 270 - Beta Canister | ✔ | ✔ | |||||
RTPØ 105, 190, 270 - Beta Liner | ✔ | ✔ | |||||
RTPØ 350, 460 - Alpha, Beta Liner, Beta Canister | ✔ | ✔ | ✔ | ||||
Service Fixtures (Vacuum, Nitrogen, Compressed Air, Nozzle for BioVap) | ✔ | ✔ | ✔ | ✔ | |||
Spray Ball (CIP) with Manual Ball Valve | ✔ | ||||||
Spray Gun (WIP) with Manual Ball Valve | ✔ | ✔ | |||||
Sterile Continuous Liner | ✔ | ✔ | ✔ | ||||
Sterility Test Pump | ✔ | ||||||
Temperature and Relative Humidity Monitoring (only for process chamber) | ✔ | ✔ | ✔ | ✔ | |||
Rear view monitor | ✔ | ✔ | ✔ | ✔ | |||
UV Lamp | ✔ | ✔ | |||||
Weighing Scale Granite Slab | ✔ | ✔ | ✔ | ||||
Sharps (inside) | ✔ |