Cell Processing Isolator: Choosing the Right Isolator for Cell Therapy
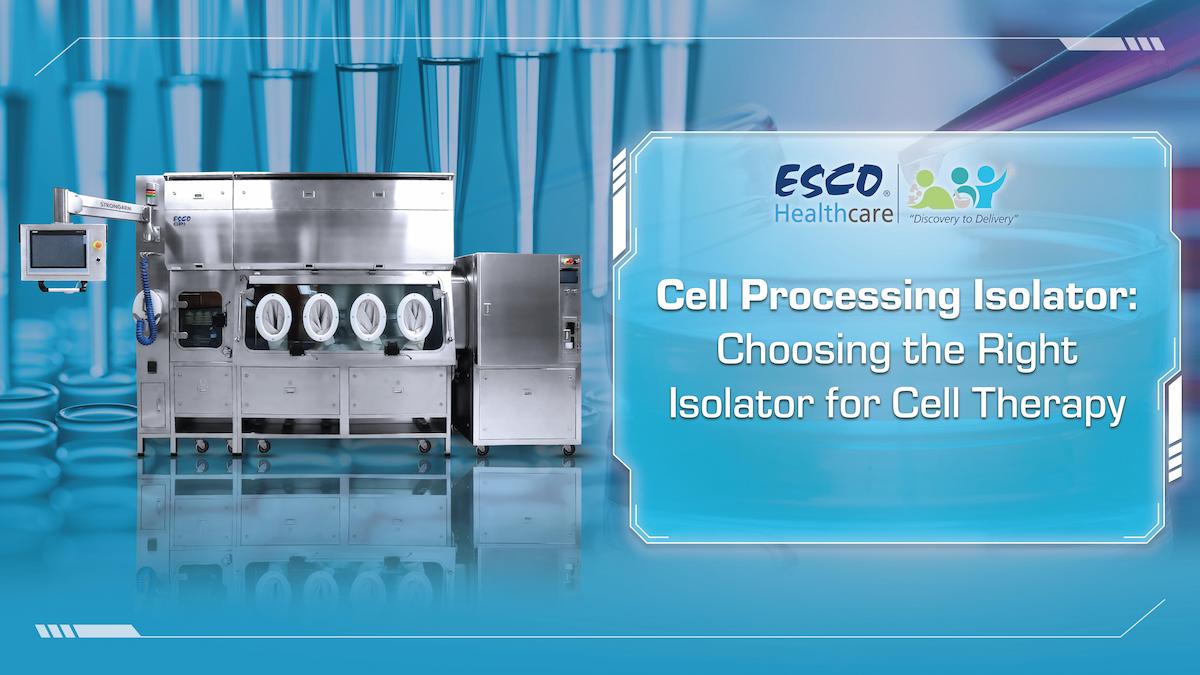
Cell processing is moving towards commercial production by scaling up
and through multiple means of increasing the capacity of laboratory processes. Automated
systems are now available for some of the cell manipulations that are
traditionally carried out manually. Some processes, however, still do not have
the available option for closed system automation.
The traditional means of using biosafety cabinets (BSCs) to provide
product and operator protection in this application are more commonly found and
suited in the initial research and development stage. However, the scale-up of
this equipment proposes a possible hurdle. Companies opt to have a room filled
with BSCs for multiple processes.
In a scale-up production, the environment in which cell therapies are handled must follow the current Good Manufacturing Practices (cGMP). There are two available options for the environment to isolate an aseptic biopharmaceutical process:
1.
An open system
like Biosafety Cabinet provides Grade A environment placed in a Grade B
Cleanroom.
2. A closed system like the Isolator delivers a Grade A environment in a Grade C or D Cleanroom.
These setups do not only mean an area of defined ventilation or
filtration system. It includes the specific type of gowning for the personnel,
regular training of personnel, and all the related standard operating
procedures (SOPs) carried out for the application.
Compared to traditional sterile pharmaceuticals, all cell therapy applications cannot be terminally sterilized. Therefore, rigorous quality control is paramount in production regardless of the batch size or product type. Whether it is a patient-specific autologous therapy or a large-volume batch of an allogeneic, off-the-shelf product, the entire process must be carried out aseptically. All the processes including final product quality control testing must be done in a manner and area that assures sterility and efficacy.
Considerations in Selecting the Right Isolator
The following factors are to be considered in deciding on the right
isolator:
1.
Process / Method
Cell processes or methods vary widely among different products. The
common cell expansion also makes use of different technologies. The isolator
must allow routine processes to be carried out in an efficient manner while
together eliminating the risk of contamination.
2.
Equipment
Integration Capability, Machinery, and Robotics
Depending on the process, the isolator’s physiological requirements and
design may vary. Isolators may be integrated with multiple sets of equipment
such as incubator, centrifuge, and microscope, among others.
The area of pharmaceuticals in which robotics are commonly used is in
the aseptic fill-finish process. Semi-automated or fully automated filling
machines may be integrated within an isolator system.
Note: Esco Pharma can customize isolators integrating the
client's process equipment. For more information, contact the local office near
you today.
3.
Ergonomics
Typically, cell therapy processes are carried out for a long-term
duration. The ergonomics of an isolator must allow manual manipulations to be
carried out efficiently and comfortably.
4.
Instrumentation
The design of the isolator must have the ability to pass samples and
data from all the instruments and equipment within the isolator and allow
connection into the possible building management system.
5.
Environment
Isolators can provide product, operator, and environment protection.
Depending on the characteristic of samples handled, an isolator may operate in
negative and/or positive pressure with a single pass or recirculating airflow
regime. It can be designed with a fully integrated bio-decontamination system.
It is also capable of providing special conditions such as an inert environment
and/or temperature and relative humidity-controlled system, depending on the
requirements.
Cell Processing Isolator
Esco Pharma’s Cell Processing
Isolator (CPI) is designed to
provide an ergonomic and practical cGMP compliant solution for the production
of cell therapies. The CPI is designed to isolate the process to ensure
operator safety, without compromising the product quality. It also provides the
unidirectional/laminar airflow delivering a sterile environment (ISO Class
5/Grade A) that is required in carrying out aseptic processes.
As a fully cGMP-compliant isolator and an aseptic containment system, it
is capable of automated pressure hold testing and of automated
bio-decontamination. It can also be equipped with a glove leak tester to allow
individual testing of the glove’s integrity. By standard, the internal material
of construction is made with stainless steel 316L equipped with passthrough
chambers. It may also be equipped with Rapid-Transfer-Ports (RTPs). This design
allows the introduction and removal of samples in a controlled material flow
without the risk of introducing contaminants into the internal chamber or
allowing the products to escape the isolator.
A CPI is also equipped with environmental monitoring capabilities such
as temperature sensors, relative humidity sensors, and pressure sensors.
Continuous particle monitoring systems and viable/microbial air samplers can
also be integrated.
The CPI is an integrated system that can combine several types of equipment into one isolated solution. This setup offers increased sterility with a reduced risk of contamination, thus increasing patient safety. The CPI can be custom-designed to suit individual customer requirements (see Figure 1). Depending on the client’s requirements, the following are the common sets of equipment that are integrated into a CPI:
·
CO2 Incubator
·
Centrifuge
·
Microscope
·
Refrigerator
and/or Freezer
·
Peltier Wells
·
Bioreactor
·
Harvesting
Systems
·
Filtration
Systems
·
Laminar Airflow
Cabinet
·
Biosafety
Cabinet
· Laboratory Shaker
Figure 1. Cell Processing Isolator with fully integrated sets of equipment for full aseptic bioprocessing
Choosing the correct system like the cell processing isolator can
provide multiple advantages. As we develop and customize the equipment and the
processes. It is also critical to note that the cost and schedule are always
the major drivers in equipment selection. The key in the selection of an
isolator is to find a machine, process, and system that best fit your process
and product.
Cell therapies are capable of giving terminal patients an opportunity to
survive. At the end of the day, considerations must be made based on the added
value that a piece of equipment or upgrade brings about to one’s
services.
References:
1. Bozenhardt, H. (2020, April 16). Selecting The Right
Isolator For Cell Therapy Manufacturing: Considerations & Challenges.
Https://www.Cellandgene.Com/. Retrieved January 28, 2022, from
https://www.cellandgene.com/doc/
selecting-the-right-isolator-for-cell-therapy-manufacturing-considerations-challenges-0001
2. European Medicines Agency. Advanced therapy medicinal
products: Overview. (2021, December 3). Retrieved February 5, 2022, from
https://www. ema.europa.eu/en/human-regulatory/overview/
advanced-therapy-medicinal-products-overview
3. Meyer, D. (2021, May 27). Individual closed isolators
for cell therapy. A3P - Pharmaceutical & Biotechnology Industry. Retrieved
February 12, 2022, from https://www.a3p.org/en/ closed-isolators-cell-therapy/
4. US Food and Drug Administration. Guidance for Industry
Sterile Drug Products Produced by Aseptic Processing – Current Good
Manufacturing Practice, US Department of Health and Human Services. Rockville,
Md., 2004. https://
www.cellandgene.com/doc/selecting-the-right-isolator-for-cell-therapy-manufacturing-considerations-challenges-0001