Esco Pharma USA Successfully Commissions a Filling Line Isolator Project
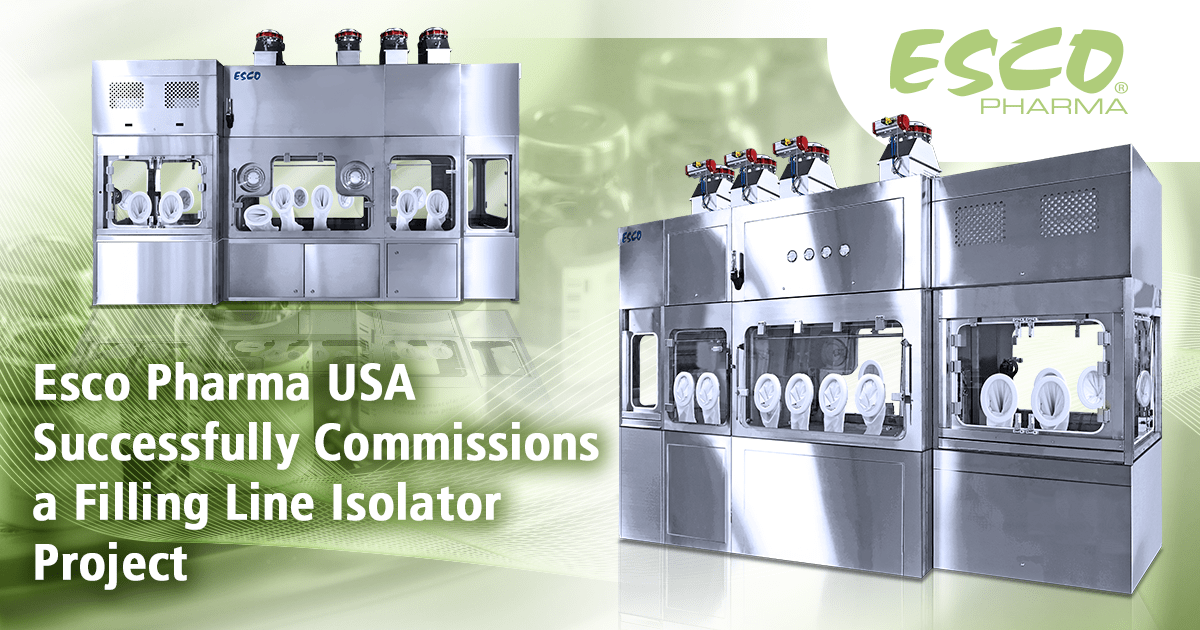
The manufacture of sterile
pharmaceuticals requires advanced technologies like filling line machines to
ensure compliance with stringent manufacturing guidelines.
Pharmaceutical filling line streamlines
the manufacturing process of medicines. It is capable of expediting the filling
of hundreds of vials, ampules, or pre-filled syringes per minute of production
while preventing product loss and ensuring consistent volume of product. It can
also facilitate continuous operation in meeting the output demands of
production. A filling line equipment can be a fully automated or semi-automated
system that offers sterility control for critical operations. This is now
becoming the standard of sterile pharmaceutical manufacturing.
Esco Pharma designs and manufactures isolation containment systems that are built around the design of the filling line equipment and customizes it to meet individual client requirements.Filling line isolators commonly enclose the filling, stoppering, and capping processes of a filling line machine. The system provides an ISO Class 5/Grade A environment and integrated hydrogen peroxide decontamination to ensure the sterility of the area and to meet the stringent demands of sterile production. Filling line system projects usually have a duration of 8 to 14 months depending on the complexity of the design and the customizations that are needed to be done.
The Project
This month, Esco Technologies Inc. (Esco
Pharma USA) finished the commissioning of its project for filling line
isolators and open restricted access barrier system (oRABS) for a
pharmaceutical manufacturing company in the USA.
The complete equipment contains the following components:
- an oRABS for the automatic bag opening process,
- a 2-glove Isolator for the automatic tub opening process,
- a 4-glove Isolator for the automated robotic filling and closing, and
-
an oRABS for the vial sealing module
The filling line system was designed
with an entry oRABS for bag removal, connected to an isolator for tub opening,
and then an isolator for the automated filling and closing of the vials.
Lastly, it connects to an exit oRABS where the capping process is carried out.
The isolators and oRABS systems were
designed to create a continuous environment that will achieve the required
operating parameters of the filling line machine. It is designed to operate in
a positive pressure relative to the ambient environment, with a suitable
pressure cascade between different modules. It also operates in Grade A/ISO
Class 5 laminar airflow conditions.
The two units of isolators are
double-wall designed with inlet and exhaust ducted out of the room to remote
HVAC skids. Both are capable of temperature control with cooling mechanisms.
The tub opening isolator is equipped with one rapid transfer port (RTP) for
waste removal. While the fill close module isolator is equipped with two RTPs,
one is for liquid transfer to the pump and the other is for charging of the
stoppers.
These isolators are also equipped with
the BioVap™ biodecontamination system with onboard hydrogen peroxide sensors
and room sensors. It is designed with remote skids for exhaust with
double-stage catalytic converters which enables the system to exhaust air back
to the building after the biodecontamination process.
The equipment and its control system
were designed and constructed following cGMP and GAMP 5 guidelines in addition
to industrial equipment directives.
Filling line isolators are designed to incorporate third-party filling line equipment. To ensure the delivery of quality products, Esco Pharma works hand in hand with partners from leading filling line manufacturers. While the process of building a filling line isolator system requires extensive planning, Esco Pharma, amplified with its experience, is consistent in bringing about solutions for worthwhile challenges.
Click here for more information about our Filling Line Isolators or
contact us at [email protected]