Inhaled Insulin: Boon or Bane?
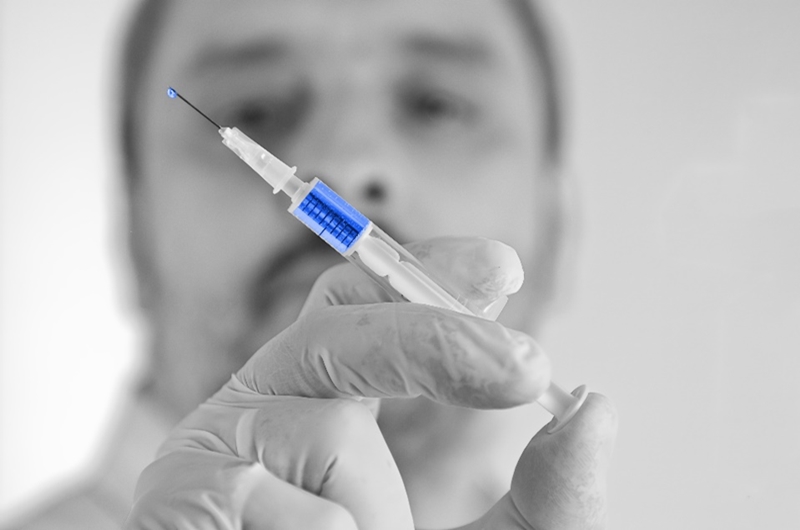
For the past few decades, pharmaceutical companies are investing on modernized ways and methods to find a viable way to get insulin into the bodies of people with diabetes without needles.
Naturally the idea of an insulin inhaler, similar to an asthma inhaler, was an appealing prospect. But it wasn’t until new technologies appeared on the scene in the late 1990’s that researchers could really begin to experiment with turning insulin into a concentrated powder with particles sized for inhalation into the lungs.
Insulin (Human) will be provided as insulin spray-dried powder, comprised of recombinant human insulin, sodium citrate, mannitol and glycine; and is presented in pre-dispensed 1 and 3 mg unit dose blisters. For pulmonary drug delivery, a reusable manually operated dry powder inhaler is used. Key functions of the pulmonary inhaler are the dispersion of powder to form an aerosol cloud (inspiratory independent) into a holding chamber and the delivery of the aerosolized powder to the patient. The insulin pulmonary inhaler is CE certified.
Description of the Manufacturing Process
The manufacturing process of the drug product consists of three steps: (1) The solution preparation and (2) the spray drying process for the manufacture of the insulin spray dried powder and 3) filling and packaging. Insulin spray dried powder is an intermediate in the manufacturing process of the drug product. The powder is stored in steel containers and shipped to the blister-filling site, where it is filled in 1mg and 3mg blisters.
In-process controls
The fermentation process, the downstream processing and purification of the expression product are sufficiently controlled by appropriate in-process controls and acceptance criteria. The efficiency of the concentration and purification steps is monitored by HPLC analysis. The structure of most byproducts has been elucidated and their removal is either demonstrated by validation data and/or limits are set for in-process control testing at the respective purification stages.
Development of the Manufacturing Process of the Active Substance
During the early development phase of insulin inhalation powder, pre-dispensed, different recombinant human insulin sources deriving from modified manufacturing processes were used for clinical (Phase 3) and development batches. Information demonstrating the equivalence between these sources was provided.
Modification and Purification
The inactivated cells are separated by centrifugation and disrupted by pressure-expansion treatment to obtain the fusion protein that is enriched by on-line washing and centrifugation steps. The downstream processing of the fusion protein to human insulin is a sequence of modification and purification steps. Sub-batches are mixed to obtain the final drug substance and stored at -20°
The rise of inhaled insulin paves the way to modernization and continuous evolution of drugs for an optimum health care delivery. Esco Pharma® offers flexible solution to comply with the innovative requirements inhaled insulin have. General Processing Platform Isolator (GPPI) is a highly adaptable, unidirectional laminar airflow isolator that can be used for sterility testing or other processes that require an ISO Class 5 (Grade A) aseptic environment. The GPPI’s advanced control system allows the operator to select either positive or negative chamber pressure as well as single pass or recirculating airflow patterns. These features, along with the ability to perform safe change procedures on the supply and return ULPA filters, make the GPPI a highly versatile isolator that can be used for potent or non-potent aseptic materials. With a company like Esco Pharma, the public can be assured that from the research and development stage up until the drugs’ final formulation on its dosage form, continuous innovation will fuel every step of drug discovery and development for an optimum health care delivery.
References:
- Amy Tenderich, Healthline: The Story of Inhaled Insulin, 2016
- Scientific Discussion on Inhaled Insulin, Exubera®. Retrieved from http://www.ema.europa.eu.