Cell Processing Isolator: A Highly Modular and Adaptable Solution for Cell Processing
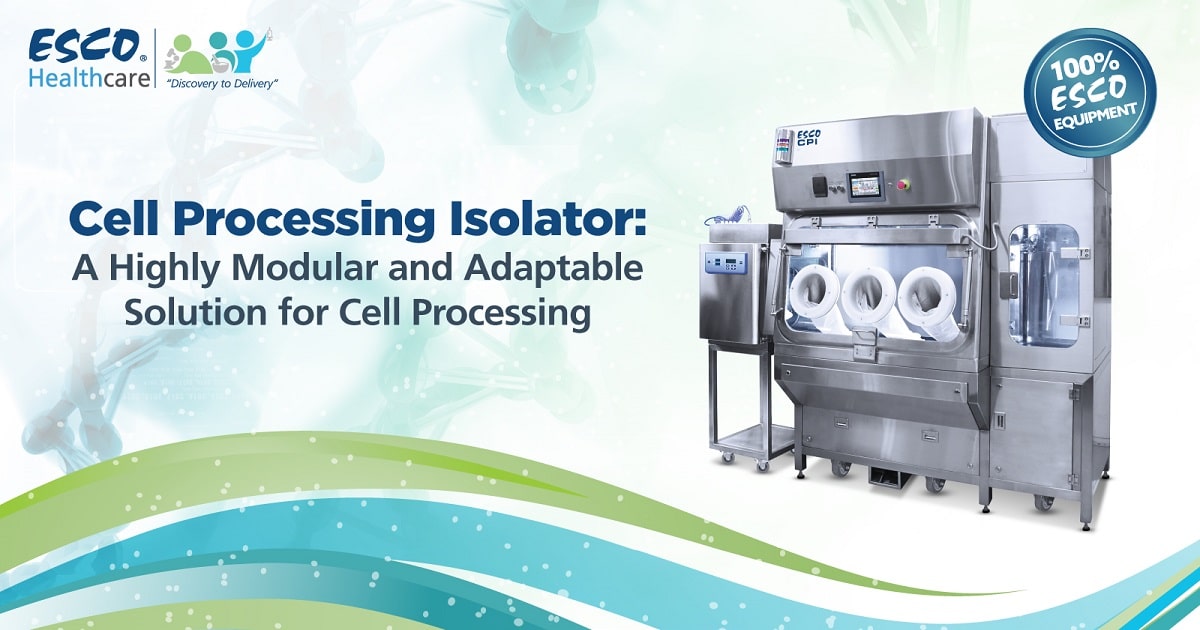
Introduction
A Cell Processing Isolator (CPI) is an integrated system that combines several types of equipment into one isolation technology.
A CPI is designed to isolate the process to ensure operator safety without compromising product quality. It also provides a sterile ISO Class 5/Grade A environment that is required for carrying out aseptic processes.
This specific isolator is designed for the following applications:
Allogenic Cell Therapy
Autologous Cell Therapy
Biosafety/Animal Biosafety Level 3/4 Containment
Cell Banking
Monoclonal Antibody Production
Phase III Clinical Trial
Protein Production
Vaccine Research
Virus Production
As a cGMP isolator and an aseptic containment system, the CPI is pressure tested and capable of biodecontamination using BioVap™ - Esco’s own hydrogen peroxide-based biodecontamination system. BioVap™ is capable of a 6 log reduction in bioburden. It is not affected by temperature or relative humidity; thus there is no pre-conditioning requirement to the chamber before use, leading to a reduced cycle duration.
Equipment Integration and Options
The CPI is highly modular and adaptable to meet the client’s requirements. General bioprocessing equipment such as a CO2 incubator and a centrifuge can be integrated into the isolator. These said bioprocessing equipment are also manufactured by Esco.
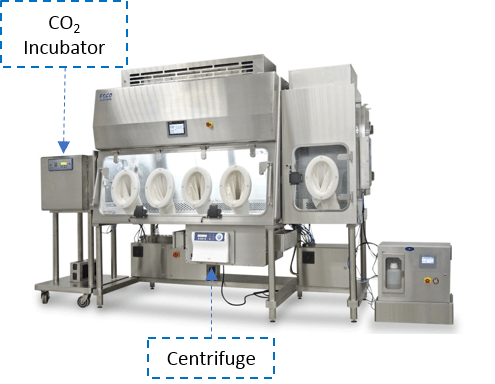
Figure 1. Isolator with integrated Esco’s CelCulture® CO2 Incubator and Versati™ Centrifuge.
The CPI can also be converted into an isolator incubator, capable of temperature, relative humidity, CO2, N2, and suppressed O2 control. CPI can also accommodate other bioreactors such as wave, shaking, orbital and other types of bioreactors.
Additional options include integration of Esco cell therapy equipment, but also as a stand-alone isolator with third-party devices (See Figure 2).
For clients requiring temperature and CO2 control, Turbulent Flow Aseptic Isolator (TFAI™) or Aseptic Containment Isolator (ACTI) can be used.
Figure 2. With Esco’s wide range of isolators, clients can easily choose their base isolator depending on their process requirements.
The advantage of TFAI over ACTI is the optional Pod Flange which allows integration of other equipment on the base and in the rear portion of the isolator. For those needing cell therapy equipment integration on the base of the unit only, General Processing Platform Isolator (GPPI) and Advanced Processing Platform Isolator (APPI) are available. While for those requiring a stand-alone unit (with own control system) connected to the isolator through electrical sockets, Esco offers the Streamline® Compounding Isolator (SCI) and the Isoclean® Healthcare Platform Isolator (HPI-G3).
CradlePRO™ Iso
CradlePRO™ Iso, is a CPI for CelCradle™ bioreactors. This includes the CelCradle™X, a ready-to-use bioreactor capable of high-density cell culture.
CelCradle™X (CCX) is a closed, automated, single-use cGMP bioreactor that is designed based on tide motion technology. CCX is equipped with its own incubation system that can be docked and undocked to the CPI’s process chamber.
CelCradle™X (CCX) is a closed, automated, single-use cGMP bioreactor that is designed based on tide motion technology. CCX is equipped with its own incubation system that can be docked and undocked to the CPI’s process chamber.CradlePRO™ Iso is easily customizable depending on the client process requirements. It can come as a 2-glove, 3-glove, or 4-glove isolator. It can also integrate a refrigerated centrifuge and a peltier in the process chamber. Its backwall also allows docking/undocking of a CO2 incubator and the integration of Rapid Transfer Ports (RTP), liquid transfer ports, or even the interconnection to other modules.
Additional options include:
-
Temperature, relative humidity, CO2, NO2, , or O2 control, as isolator incubator
-
Microscope integration
-
BioVap™ biodecontamination system
-
Viable and non-viable particle counter integration
-
Glove Leak Tester
-
Flexible visors
-
Ability to operate as anaerobic glovebox
The Project
Esco was recently commissioned to manufacture a Cell Processing Isolator(CPI) for a national biopharmaceutical institution: a contract manufacturing facility that aims to produce clinical research grade biopharmaceuticals. This model was intended specifically for virus seed production.
The main challenge for this project was to produce an isolator system fully integrated with a 58-L CO2 incubator, a refrigerated centrifuge, and a waste disposal port; while maintaining a compact sized unit to easily fit inside a small facility.
A cGMP-compliant design was of great importance to the client, as it was part of the facility’s innovation platform.
The commissioned CPI unit was made entirely from stainless steel, with SS 316 L interior and SS 304 exterior. It was designed with a flat base with easy access doors made from laminated tempered glass. Its glove ports were made from polypropylene fitted with CSM gloves.
It is capable of carrying out pressure decay tests, biodecontamination, as well as auto-compensation, enabling the unit to adjust and maintain the required negative pressure environment. Through this mechanism, It ensures process containment and operator protection in cases of breach in the system.
It is capable of carrying out pressure decay tests, biodecontamination, as well as auto-compensation, enabling the unit to adjust and maintain the required negative pressure environment. Through this mechanism, It ensures process containment and operator protection in cases of breach in the system.
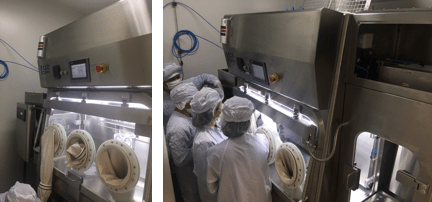
Figure 3. CPI installed in the facility
Additional features include:
-
Pass-through Chamber: allows quick access and easy transfer without breaking chamber containment and sterility.
-
BioVap™ biodecontamination system: hydrogen peroxide-based biodecontamination system
-
Airborne and viable particle counters: allows airborne monitoring of chamber cleanliness
-
Built-in stainless steel refrigerated centrifuge: operates through foot switches for start/stop operation and for deflating the inflatable sealed cover.
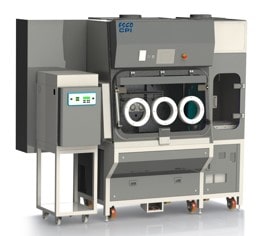
Figure 4. Cell Processing Isolator’s 3D Image
Cell Processing Isolator Project Timeline
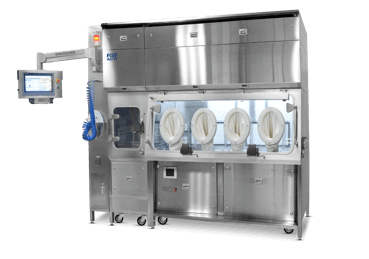
Aseptic Containment Isolators (ACTI)
2016-2017
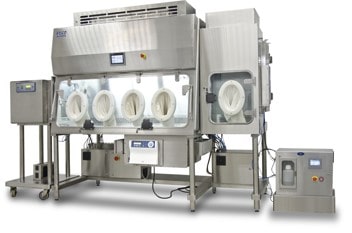
Advanced Processing Platform Isolators (APPI)
2018
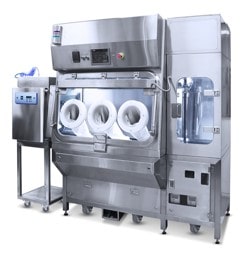
Cell Processing Isolators (CPI)
2019
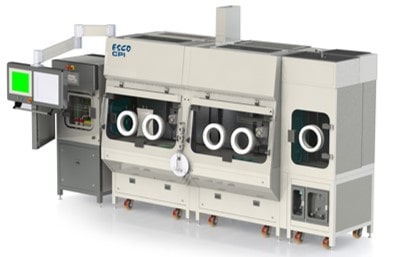
Cell Processing Isolators (CPI)
2020
Over the past few years, Esco has had the opportunity to handle numerous isolator projects for cell processing application. It was only recently that the company decided to create a new line of isolators specifically for bioprocessing under the category of Cell Processing Isolators.
Equipment customization and integration is made easier due to Esco being a world leader in manufacturing life science equipment.
Esco VacciXcell, the bioprocessing division of the company, also has its own bioreactor systems, that makes customization and equipment integration even easier to accommodate.
For more information, please visit our page for Cell Processing Isolator (CPI).
Esco VacciXcell Bioreactors
There are different types of bioreactors available in the market and choosing the right one is crucial in the success of your culturing process. Choosing the right bioreactor system for your application highly depends on the type of cells to be produced, the desired product, the process of the cell culture, and the product density.
Esco VacciXcell offers different types of bioreactors, specializing in adherent cell culture linearly scalable from laboratory to production scale.

CelXRocker
Process Optimization of Cells in
BioNOC™ II Carriers
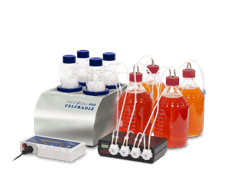
CelCradle™
Cradle for High Adherent
Cell Density
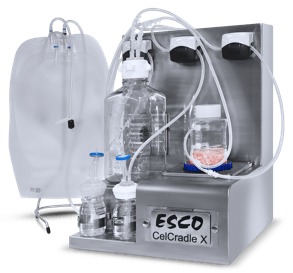
CelCradle™X
Closed Automated Single-Use
cGMP Bioreactor
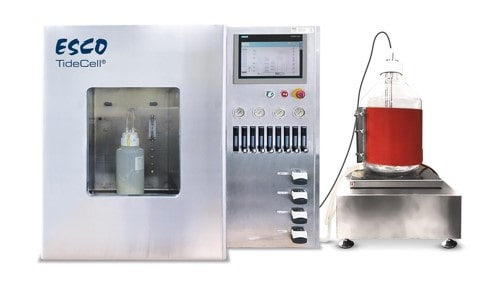
TideXcell™
The Gentle Giant of Adherent Bioprocessing
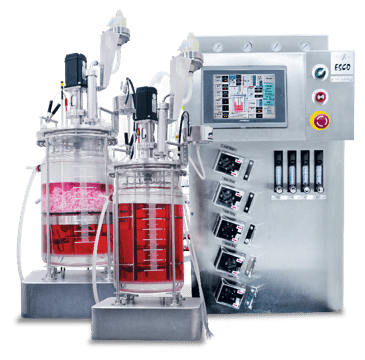
The VacciXcell Hybrid Bioreactor
Versatile Bioreactor
For more information about bioreactors, please visit www.vaccixcell.com